Drilling - How It Works
Drilling a Borehole: Understanding the Process
Each borehole drilling project presents unique challenges; no two boreholes are exactly alike, and many years of experience has prepared us to tackle any scenario that is presented to us. Here's a general guide to how the process works for drilling an average borehole:
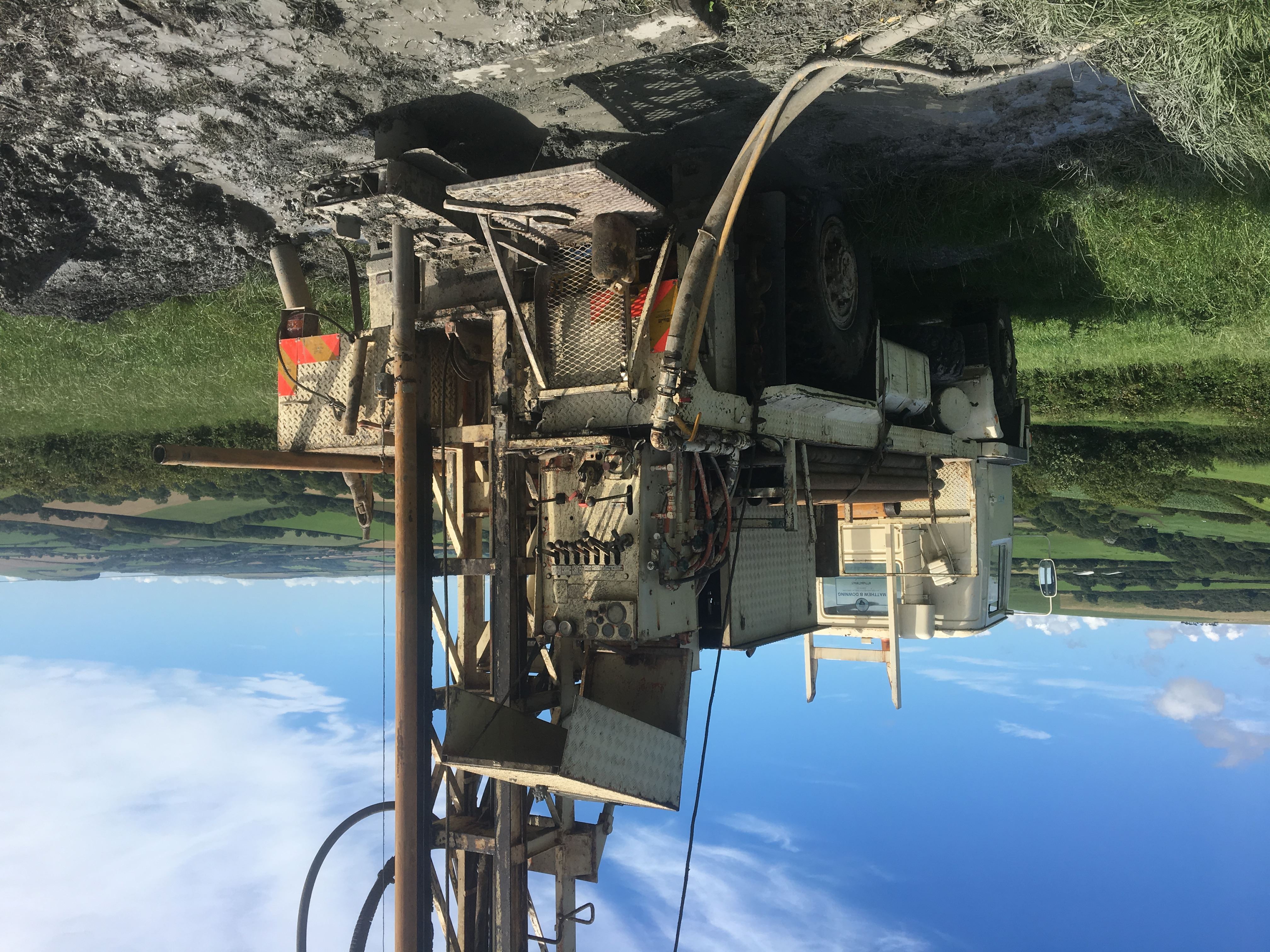
Equipment
The size of the drilling rig varies based on the hole's depth and the site's geological conditions. We select drill bits according to the type of geology. Commonly, we use a Rotary PCD (PolyCrystalline Diamond) drill bit for soft to medium soil, and a DTH (Down-The-Hole) hammer for rock formations. Our operations also involve the use of a CompAir Turboscrew compressor.
Drilling the Borehole
Our process begins by drilling a 200mm hole. Initially, we drill the first 3 metres, then drill in a 1.5-metre length of 200mm steel casting. This step secures the borehole against soft, shifting surface soils.
We employ compressed air through the drilling rods and out through the drill bit – a critical step to clear the hole of debris. If we encounter shifting layers, sands, or voids, we continue with the steel casting until we reach stable geological strata.
As we drill, we gain a good understanding and insights into the geology, water presence, quantity and yield. We only proceed to install the well-liner when we’re confident that the water quantity is suitable for our client’s needs.
Lining the Borehole
Selecting the appropriate rig, drill bit, and maintaining borehole stability are crucial, as important as installing the correct well liner. The right liner enhances the water well's performance, prevents collapse, and guards against water contamination.
Among the many available linings, the one we use most frequently is made from PVC (it’s certified by KIWA, DWi, and WRAS, and ISO 9001 Quality Assured).
While drilling, we identify where we have located the various aquifers, allowing us to strategically place the perforated liner to maximise water intake.
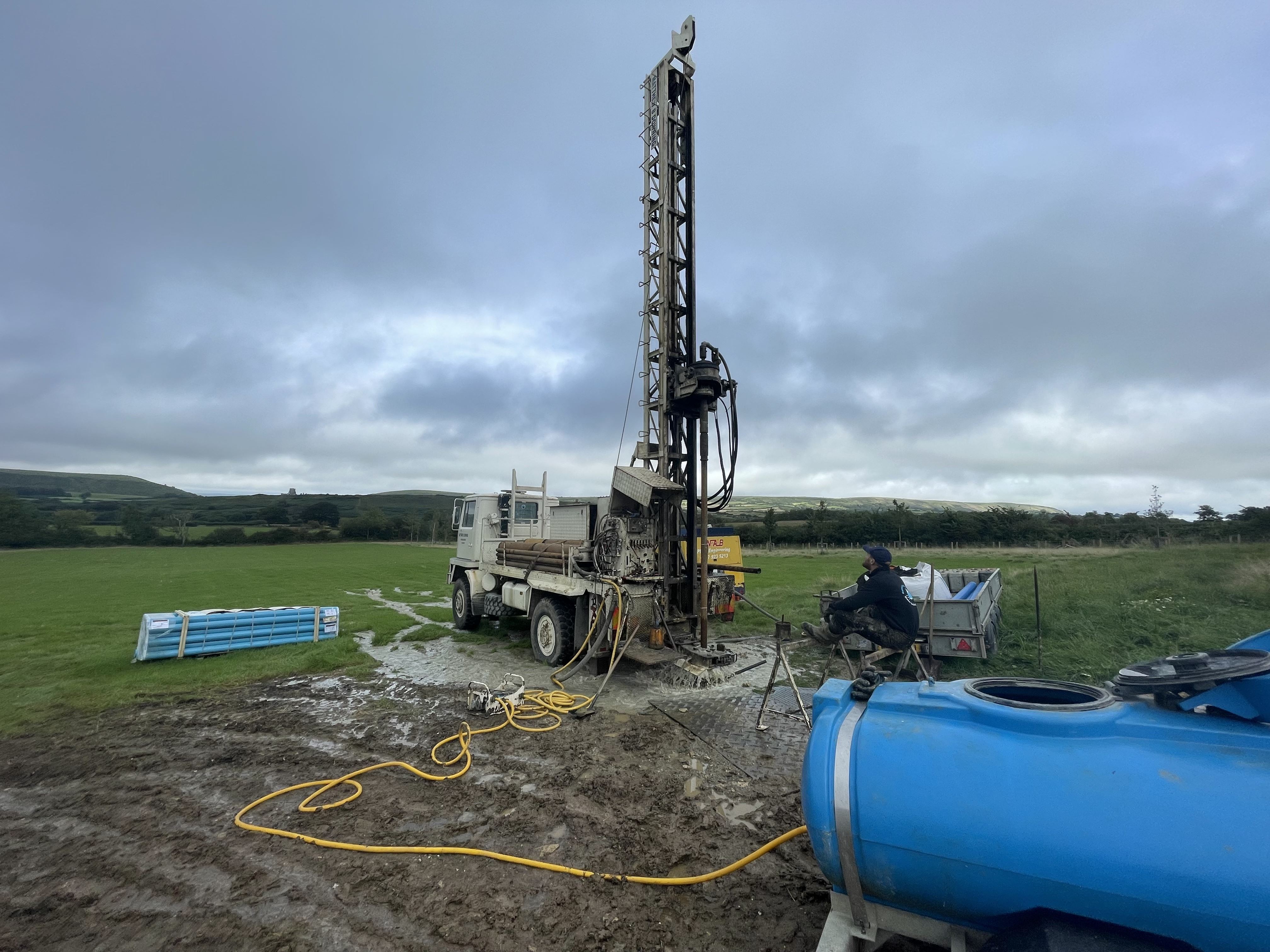
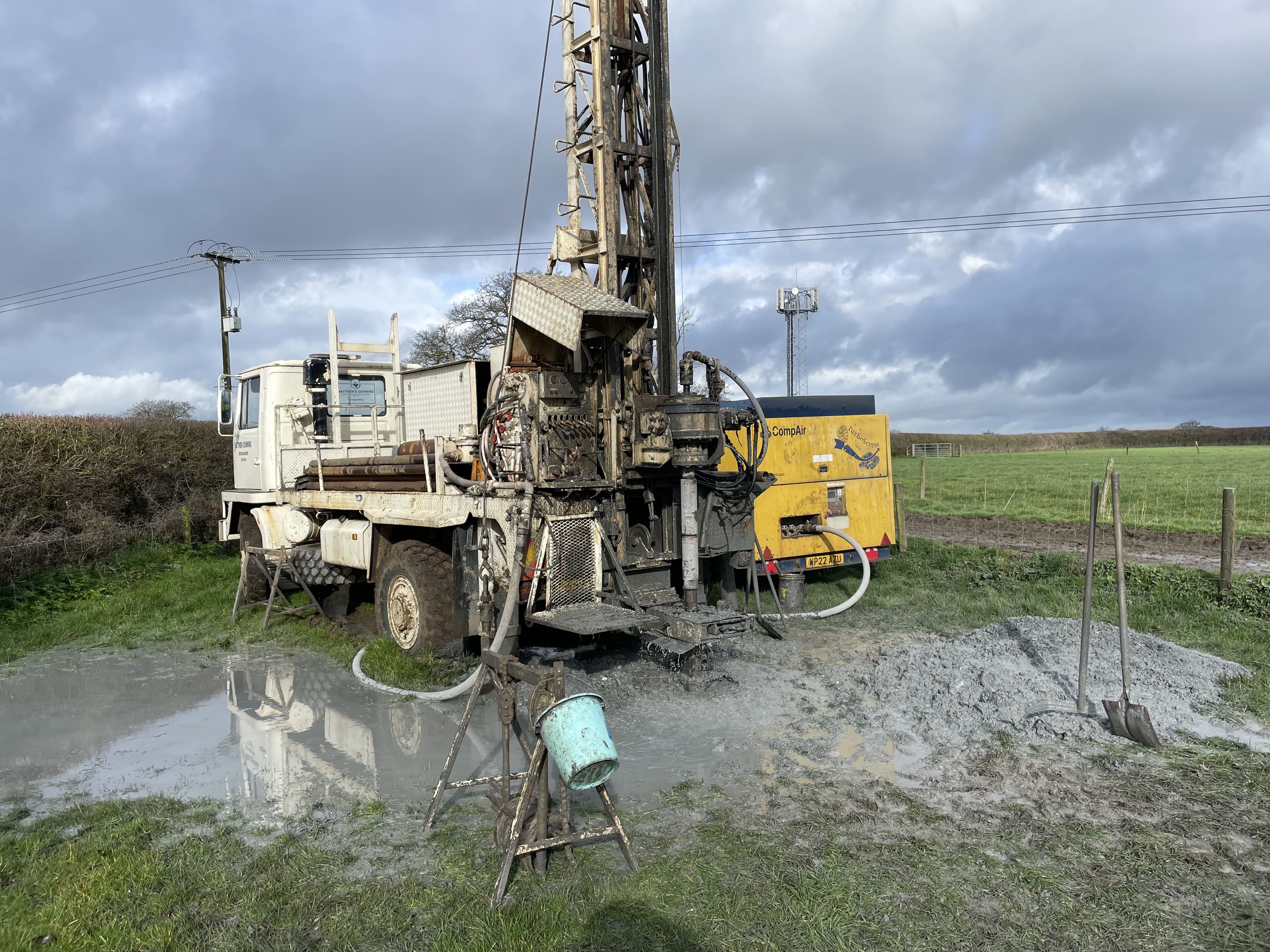
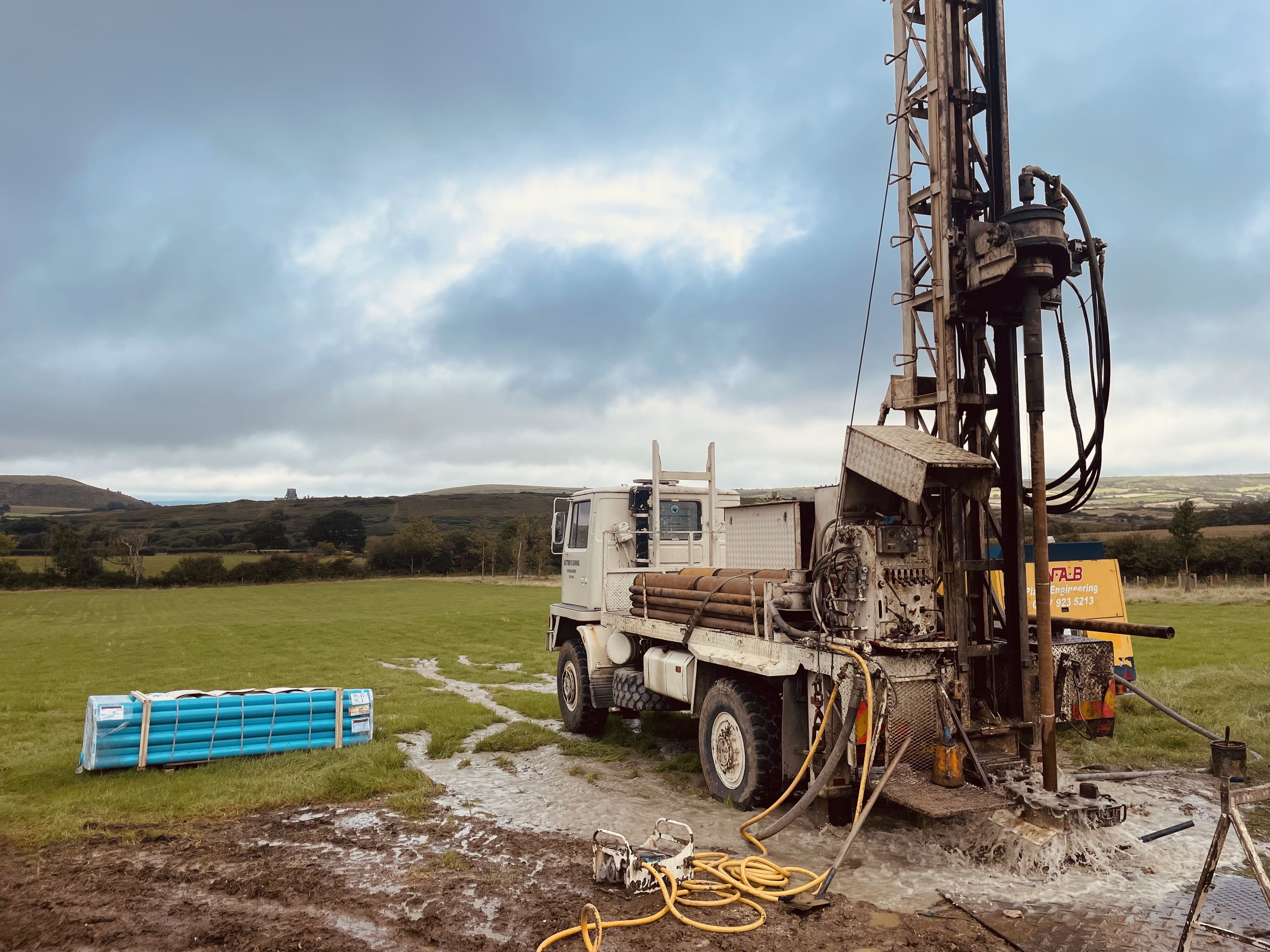
Filter Pack
The final step is installing a gravel filter pack. This goes on the inside of the 200mm drilled hole and the outside of the 125mm well liner. We typically use 8-10mm rounded pea gravel, and for sealing, bentonite is employed. Carrying out this stage correctly is crucial for protecting the well liner, facilitating water flow, and enhancing the well's longevity. The bentonite seal prevents surface water from contaminating the fresh water below.